New regulations on fire safety won’t stop another Grenfell if we’re still not properly applying the old ones
Three months on from the Grenfell Tower tragedy, and the public inquiry is about to begin. Debate continues about what caused such a disaster to happen, and the desire for answers from the victims’ families is understandably strong.
The inquiry will play a crucial role in identifying the contributing factors to the fire, and I hope will help rebuild public confidence on fire safety and building regulation. Until it reports its findings, there remains a vacuum of uncertainty in which a rush for answers may lead to flawed conclusions and a very real risk of misinforming future policy.
Fire safety is an extremely complex area. Any sensible assessment of what happened at Grenfell needs to consider a wide range of factors, including building height, sprinkler installation, fire and smoke detection, means of escape, and flammability of building contents, as well as the combination of materials used in exterior walls and internal finishes. Most critically, it must review and assess whether existing safeguards are being applied and overseen, before bringing in new ones.
The potential contribution to the fire of elements of the ventilated rainscreen system (often described as cladding) has been the subject of widespread public comment: in particular, the use of polyethylene-cored aluminium composite material (ACM) panels on the building’s exterior.
We must improve its knowledge base of how all these different elements interact
So far as I am aware, polyethylene-cored ACMs have never been successfully tested in a cladding system in a manner consistent with building regulations, so it is hard to understand how this product ever ended up on Grenfell Tower. Similarly, given the fire performance characteristics of these ACM cladding panels, it is no surprise in my view that they performed so poorly in combination with a range of insulation types in the recent series of large-scale tests by DCLG.
Trusting in simplistic classifications for materials based on small scale testing (such as Euroclass categories or a ‘non-combustible’ label) is not the solution. The reality is that a whole range of factors will affect fire safety, including the design of cavity barriers, fixings used and cavity width. We must improve our knowledge base of how all these different elements interact. As any fire expert knows, even ‘non-combustibles’ are still capable of burning and, in isolation, are no guarantee of what constitutes a fire safe building.
This reinforces the legitimate public concern about whether current building regulations are fit for purpose. Whilst we should avoid a rush to new rules, I believe there are four areas where changes could be made for the better:
First, large-scale testing under BS8414 should be extended to cover all cladding systems whether they include combustible, non-combustible or limited-combustibility components. System testing is crucial to understand the way that all materials in a roof or wall interact with each other, and there should be no automatic or linear route to compliance for certain materials. The fact that both PIR and mineral fibre insulation failed the recent DCLG tests in combination with a PE cored ACM demonstrates that relying on a ‘non-combustible’ label is not enough, and the focus needs to shift to a system performance based approach.
Secondly, we need to strengthen the way desktop studies (DTS) are used in fire safety compliance, but should be conscious that they still have an important role to play: this is because performing a large-scale test on every one of the possible combinations of materials is impractical and there is not enough capacity within the testing system to allow it to happen. Improvements that can be made include having a published register of all approved desktop studies, setting mandatory qualifications for those performing desktop studies, and better prescription of what test data can and cannot be considered in the production of a desktop study.
We need better control of fire safety through the design and construction process of buildings
A third change is in the training provided for installers of building facades. Poor quality installation can compromise the safety of a building and I believe that fire-safety considerations should be incorporated into all training courses involving modern façade construction. Only accredited installers/contractors should be allowed to work on façade construction projects.
Finally, we need better control of fire safety through the design and construction process of buildings. There is no point in developing regulations unless we rigorously police that regulations are being enforced. Ensuring building fire-safety is kept front and centre throughout the process is a challenge. The Royal Institute of British Architects (RIBA) Plan of Work, which incorporates fire-safety at the appropriate stages, is a good model, but building control or approved inspectors should have to ensure that what is built matches the approved design.
Like the whole issue of fire safety it’s highly likely that the answer to the question – what caused the Grenfell Tower fire? – will be complex and multi-layered. Alongside all responsible stakeholders in the industry I am committed to Kingspan playing its part in trying to ensure that this disaster is not repeated, and that the lessons learned help ensure safer building practices in future.
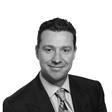
No comments yet